Polished concrete floors treated with FGS HARDENER PLUS last longer than conventional concrete floors, cost less to maintain, reflect light better, hold a shine longer, are safe to use, and are guaranteed to resist dusting for a minimum of ten years. FGS HARDENER PLUS is a water-based, VOC-compliant, odorless and environmentally safe component of this process.
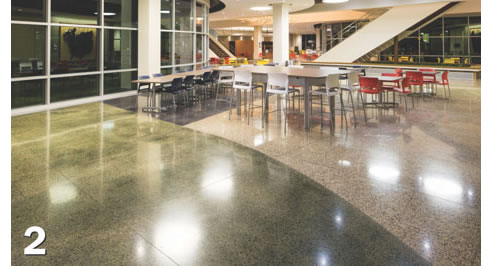
Award winning floor: L&M's fgsPermaShine polished concrete floors help Burgess Concrete Construction and Gordon Food Service earn two prestigious honors.
Burgess Concrete Construction is a full-service concrete contractor. Burgess performs everything from footings in the ground to foundation stabilization to mix designs to placing concrete to polishing the finished product.
Burgess markets include K-12 schools, universities, commercial and industrial buildings. While Burgess gets a lot of repeat business and word-of-mouth referrals, they also actively market their full-line of concrete contracting services to architects and specifiers, general contractors, and engineers. They target the design community specifically for mix designs and polished concrete.
Burgess's marketing and proven track record created an exceptional professional reputation in the flooring space. Architects and specifiers know their work. Engineers know their work. General contractors know their work.
Sales Manager Tim Burgess took the project architect and owners to locations of Burgess's past concrete projects. The owner liked what he saw and selected Burgess Concrete for the job.
This new construction project was a design-build for the concrete placement and polishing. The owner had an idea of what they wanted-something unique-and Tim's team helped to make their vision come to fruition. It was a collaborative effort, from the initial design all the way to the polishing.
Due to the nature of the unique floor designs, Burgess performed several samples for the owner. They drew-up various mix designs for the project and showed them different colors and depths of grind of the polishing. Initially, they decided to use glass as aggregate, but after they performed an Alkali Silica Reaction (ASR) test, the test sample produced undesirable results. So, they decided to use alternate aggregate.
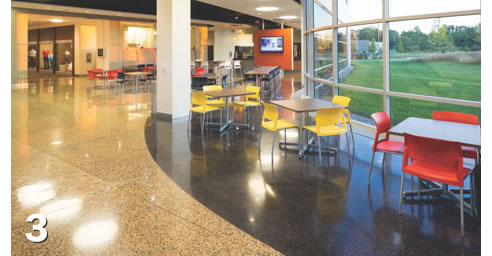
Then, they presented several different-sized stones and aggregate-types to the owner. After several suggested samples, they decided on a 2-inch limestone and 5/8th-inch heavy coarse aggregate natural stone mix.
Burgess explained that what made this concrete project difficult was placing the unique mix design on metal decks. Burgess needed to pour and place the concrete in a way that they knew the aggregate would be consistent, and then consolidate it at the edges to match the tile. Burgess employed terrazzo strips to separate the differing aggregate appearances. Working in sections, the Burgess team was able to place the unique concrete properly according to the specification.
After the concrete cured, Burgess began the FGS PermaShine polishing process. Working the set of steps in room modules, they began polishing in the basement. They started grinding the surface with 40 grit metal bonded segments. Then, 80 grit metal bonded segments. Then, 150s. Next, they moved onto the resins: 60s, 80s, 100s, 200s, 400s, 800s, to a 1,500 grit finish. After the 400s, Burgess dyed the concrete using L&M's Vivid Dye. The owner picked a custom olive green and black for its floor colors. After putting down the Vivid Dye and cleaning the excess dye from the surface, they hardened and densified the floor-and locked-in the dye-using FGS Hardener Plus. They then put down L&M's Petrotex guard product to protect the floor from spills, and finally burnished the floor to really make it pop.
From the initial pour to polishing the floor to a 1,500 grit level, the project took 6 months and approximately 2,000 man hours.
Burgess says the number of samples they showed the owner is one of the keys to success on this concrete project. "We performed lots of samples for them. We showed them many different types of aggregate. We also showed them what we are capable of with our track record of successful concrete projects by showing them floors we had polished in the area. This gave them confidence in our abilities. Since we performed so much of the pre-construction work, we felt there was little chance of losing the project to a competitor."
Burgess continued, "It's incredible how well it turned out. All this concrete is on metal decks, at different depths based on aggregate type and size, which made the placement very tricky. We had to figure out how to place 2-inch stone on metal decks. These guys really wanted a unique floor that had to be consolidated right up to the tile. We learned what we were capable of. We learned how much you really can do with concrete. There's nothing that would intimidate us after this. We made deep aggregate happen."
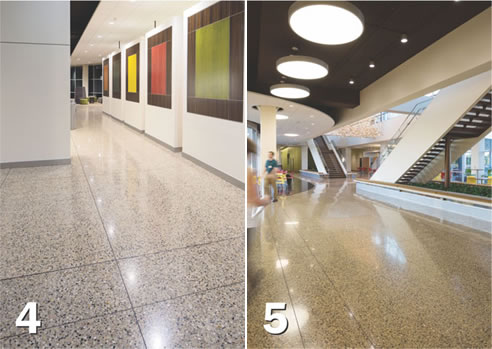
Burgess feels you can accomplish anything with polished concrete. It makes a floor that everybody talks about. This floor was a true construction team effort: from the design phase to the multiple mock-ups to the various mix designs to the actual placement of the concrete to the polishing, many project teams were involved, many meetings held, many samples and mock-ups created, and many stakeholders had a say.
Gordon Food Service's floor is an award-winning FGS Permashine polished concrete floor. It won the 2013 ABC excellence in concrete construction and the 2013 ASCC award for polished concrete over 5,000 sq ft.
Thank You to Gordon Food Service for allowing us to be a part of your winning facility.