Epoxy Floors for Commercial Kitchens from Ascoat Contracting
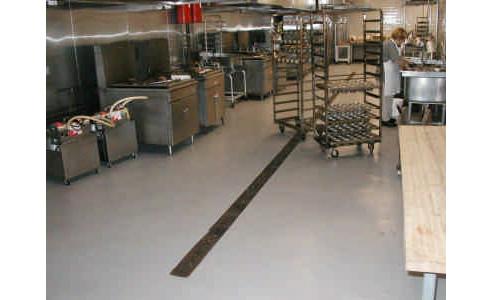
The Hyatt Regency Chicago, with over 2,000 guest rooms, is one of the largest hotels outside of Las Vegas in the United States. It has seven large kitchens to handle the massive food preparation and catering needs of its guests, as well as seven on-site restaurants and numerous conferences and ballroom activities.
All of the kitchens are run 24 hours a day/7 days a week, with thousands of meals served daily.
Built in 1974, all seven kitchens were operating with the original quarry tile floors. 30 years of operational wear and tear revealed a patchwork of different colored tiles throughout the various kitchens and an even bigger problem - water leaking from kitchen floors into lower level exhibit rooms. Leaking floors were causing not only sanitation and maintenance predicaments,
but serious complications for the hotel staff and its guests.
Stonhard's local Project Manager worked with the Facilities Engineering Department at the hotel and evaluated the floors. To temporarily correct the leaking cracks in the existing quarry tile, the hotel's Facilities Engineering Department had been continuously replacing old tiles. Key problem areas were typically found near:
- Steam Kettles
- Cook Lines
- Stock Pots
- Dishwashers
- Ice Machines
It is common for hotels to have kitchens on various floors of the facility, with many hotel kitchens located on the top floor and/or
in penthouses. Any leak, whether major or minor, will cause problems with maintenance, sanitation, structural integrity of the
building and aesthetics.
Most importantly, these problems can adversely affect guests' experiences and negatively impact the reputation of the hotel.
For years, the Hyatt Regency Chicago's facility engineers struggled with the second floor kitchen leaking into exhibition spaces.
Stonhard approached the engineering department to discuss a solution for the problem. The hotel's initial concern was shutting down and budgetary constraints. Stonhard provided a solution that addressed both the down time issue and financial
restrictions.
After numerous discussions, and with an endorsement from the Hyatt in Atlanta, Stonhard was given an opportunity to repair 400 sq. ft. of floor under the steam kettles. This area, which was constantly subjected to thermal shock, exhibited the worst cracking. The tile, along with the grout bed, was removed and replaced with Stonset TG6, a quick-setting grout and Stonclad UT, a textured mortar system. This solution was put into service, and effectively solved the problem.
Due to this success, Stonhard was contacted to examine the floor under the cook lines and ice makers and proposed replacing the floor in the entire kitchen instead of segmented areas every year. Again, Hyatt resisted closing a high-volume, high-revenue kitchen for any length of time.
To ease their concerns, Stonhard proposed a detailed and concise installation schedule to remove the tile and grout. Concrete was
proposed to meet the budgetary concerns regarding the use of Stonset TG6.
Hyatt's management team, including facility engineers, corporate
management and chefs, were involved in the decision-making process. The poor aesthetics and disturbance of patrons due to the leaking ceiling in the conference room justified the time, cost and inconvenience of shutting down the kitchen for almost three weeks. The coordinated efforts of Hyatt and Stonhard enabled an efficient and cost-effective installation which put an end to
the repeated shut downs for repairs that had created loss of service and interruption of guest activities throughout the years.
The project was scheduled during the month of January - the least busy month of the year for the Hyatt Regency Chicago. Equipment was removed by Hyatt Regency's engineering staff and all meals scheduled for preparation in the main kitchen were distributed among the other six kitchens. Stonhard's crew removed all existing tile and grout. A sub-contracted concrete company cut out and reset the drains and then poured fresh concrete to rebuild the height and pitch of the original floor.
After a seven day cure, the concrete was blasted and 7,200 sq. ft. of Stonclad UT was installed. From demolition to completed
floor installation, the project took 23 days.
Due to this project's overwhelming success, plans are underway to replace all six of the remaining kitchens at the Hyatt Regency
Chicago. Each remaining kitchen floor will be replaced on an annual schedule in the years ahead.
|
Ascoat Contracting Profile
03 9587 7433
80 Industrial Drive, Braeside, VIC, 3195
VISIT WEBSITE
|