Decorative Ceramic Tiles: How They Are Made from Designer Ceramics
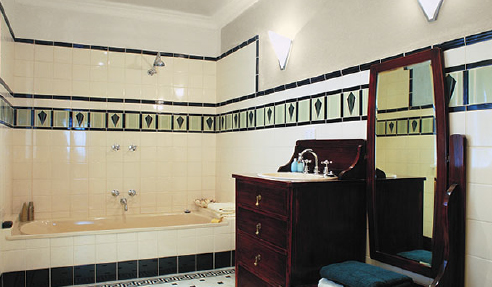
The use of decorative ceramic tiles can be traced back to the creation of clay roof coverings centuries ago. Decorative tiles have been used by different civilisations from the early Egyptian period, Babylonians, Ottomans, and 14th century Europe.
As civilisations evolved, technology evolved with it.
Today, decorative ceramic tiles have become the material of choice for interior designers, architects, and homeowners. Ceramic tiles are popularly used for kitchen splashbacks and bathroom walls. Aside from their visual appeal, decorative tiles have additional benefits, such as the following:
- Decorative ceramic tiles can stand humidity.
- Decorative tiles are fire resistant.
- Decorative ceramic tiles don't fade.
Designer Ceramics specialises in period decorative ceramic tiles. From Victorian, Edwardian, Art Deco, French provincial, and even customised designs - Designer Ceramics has got you covered!
Designer Ceramic's period ceramic tiles are 100% manufactured in Australia. They use both manual and mechanical processes to produce high-quality embossed decorative ceramic border tiles. Manufacturing border tiles requires mostly manual labour due to the tiles' complex shape. However, basic equipment for forming, glazing, drying, and firing, which is supervised by employees are utilised for time efficiency and to ensure the quality of tiles produced.

A rundown on how ceramic tiles are made.
Most tiles are formed by dust pressing techniques. An employee deposits a batch of mixture into a mould. The mould's cavity is in the shape of upside down tile. A press descends applying both heat and pressure. This process compresses the mixture into the cavity, solidifying the tile shape and design. As the press rises, the moulded ceramic tile is manually removed and laid on a flat surface - waiting to proceed to the next process.
Tiles ready for glazing are laid out on a conveyor belt. The bell or waterfall method of glazing uses a stream of glaze that falls or sprays onto the tiles as it passes on a conveyor underneath. The tiles are then arranged in line on a flat, wooden board which is then stacked on a rack to dry. Drying of tiles usually takes several days. This process is used to eliminate excess water at a slow rate in order to prevent shrinking and cracking.
Dried out decorative ceramic tiles must be heated to strengthen and achieve their desired porosity. The ceramic tiles are then loaded into gas-powered kilns to "bake". This process usually takes 14 hours to complete. Any sudden change in temperature will result in thermal shock and will crack the tiles. Firing often starts at a standard 200 degrees Celsius, climbing gradually to a maximum temperature of 1,075 degrees Celsius and slowly going back to its starting temperature.
The cooling period takes about an hour. Once complete, decorative ceramic tiles are hardened and ready to be painted in the required colour.
For paint to stick well onto the material, each moulded tile needs to be brushed clean to remove excess dust and particles. A water-based paint that's specifically designed for ceramics is continuously mixed in the vat to keep the paint well blended. The painting process resembles an automatic car wash. The tiles travel through four spray zones each of which applies a thin coat of paint. The tiles pass under powerful heating elements which dry the paint in seconds.
After the paint has dried, ceramic tiles go through a quality check. They are hand-packed and labelled correctly ready for shipping and installation.
At Designer Ceramics, the production process has been modernised but the hands of expert craftsmen are still necessary to provide the best quality. Attention to detail, design, and local manufacturing is still the cornerstone of which Designer Ceramics takes pride in.
For more information on decorative ceramic tiles, contact Designer Ceramics on (03) 9471 0230 or visit their website at www.designerceramics.com.au today.
|