Practical External Rendering Advice from JPS Coatings
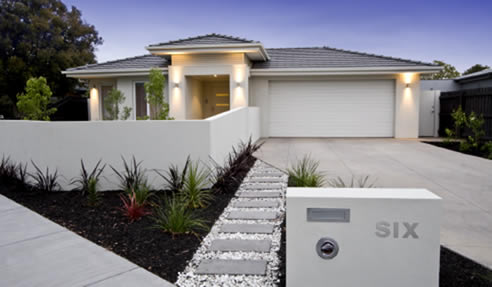
Transforming a home's facade with external rendering adds value and street appeal. Aside from enhancing the appearance of the walls, external rendering also protects the structure from natural elements such as the wind, rain, frost, and sunshine. It also keeps the structure well insulated.
Ready to Render? JPS Coatings offer what you need for your rendering application!
JPS Coatings offer a broad spectrum of tools and materials such as Dry Mix Renders, Polymer Renders, Trowel-On and Roll-On Texture Coatings, Primers, Membranes and the CodeMark certified Cova-Wall® Polystyrene Cladding System.
External Rendering Application with Dry Mix Renders from JPS Coatings
With JPS Coatings premixed cement-based renders, external rendering applications are hassle free!
1. Prepare the Substrate Wall for External Rendering
If the walls are previously rendered but have started to deteriorate, start preparing it by cutting or scraping the old render away. After removing the old render, wet the walls using a garden hose.
For new external rendering application, preparing the substrate is much easier. Make sure that the substrate wall is intact, clean, dry, and free from any residue such as oil, powder, dust and bond breakers, which might affect the adhesion of the rendering material.

2. Mixing of Rendering Product (JPS Coatings Dry Mix Renders)
Traditional rendering is done by combining four key ingredients: lime, cement, sand and water. Today, premixed renders are readily available for efficient and quick application. These rendering materials only need water to make the rendering mixture. JPS Coatings have a number of Dry Mix Render materials with different mixing solutions.
Pro-Render Acrylic Modified Render is mixed with approximately 4.5 to 5.0 litres of clean water to achieve a lump-free consistency. For each bag of Pro-Render (15 kg) the amount of water needed should not exceed 5.3 litres. Make sure to mix Pro-Render with a power stirrer thoroughly.
Polyboard Render weighs in at 20 kg per bag. The required volume of water ranges from 5 to 5.5 litres; any excess water may lead to delamination, cracking and surface crazing. Stir the mixture until the desired thick and creamy consistency is achieved. Let it settle for 5 to 10 minutes and stir it again.
Ezi-Build Acrylic Modified Hi-Build Render comes in a 15 kg bag. Pour the dry render in a clean and dry bucket and mix 4 litres of water. Using a power stirrer or similar mixing device, thoroughly mix Ezi-Build to get the correct lump-free, creamy consistency. Depending on ambient temperature, the amount of water may vary but should not exceed 4.6 litres.
Patch 'Em Up Acrylic Modified Render is available at 20 kg per bag. Mix it with 5 to 5.3 litres of water to obtain the preferred consistency. Applicators can add in water but not exceeding 5.5 litres to avoid surface crazing, delamination and cracking.
Fastwall Acrylic Modified Render weighs in at 20 kg per bag and requires 4.5 litres of water. Total water should not exceed 4.8 litres for one bag of Fastwall.
3. Rendering Application
For Dry Mix Renders, apply the render using the hawk and trowel as forcefully as possible to ensure that it adheres to the wall. Smooth the render across the wall using the trowel starting from the bottom surface going upward in a single layer. Optimum results are achieved when the render is applied in 4 to 8 mm thickness layer.
4. Drying or Curing Times
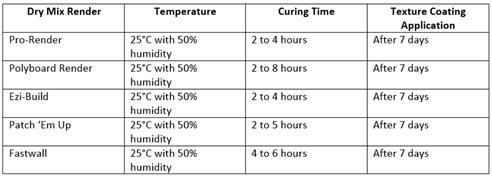
Whether it is an external rendering or internal rendering application, the key to getting the best results is to apply the correct thickness and to wait patiently for the curing or drying time.
Rendering requires some degree of skill and plenty of practice. JPS Coatings is more than happy to assist you in getting your external rendering job done!
For more inquiries on external rendering application and theproduct range, call JPS Coatings at 1300 577 262 or visit their website at www.jpscoatings.com.au today.
|