Expanded Polystyrene Foam Recycling: The Foamex Way
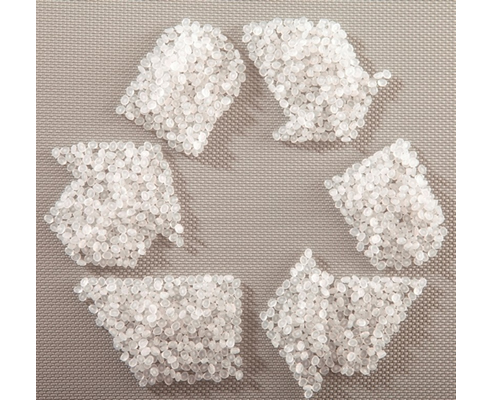
With a track record spanning more than three decades, Foamex has developed their own set of expanded polystyrene foam recycling processes to improve cost and energy efficiency, as well as sustainability in all stages of building and construction.
Foamex believes that sustainability and efficiency go hand-in-hand. Which is why Foamex adopted new measures that are eco-friendly and economic at the start of production.
In-Depth: EPS Manufacturing and Expanded Polystyrene Foam Recycling Process at Foamex
The traditional manufacturing process of polystyrene materials relies heavily on the use of chlorofluorocarbons (CFCs) and hydrochlorofluorocarbons (HCFCs). Both are a highly recognised source of greenhouse gases that are damaging to the ozone layer.
Foamex produces polystyrene products using pentane, a non-CFC (chlorofluorocarbons) expansion agent. The slightly volatile liquid is formed in a continuous natural process like the anaerobic decomposition of a fruit matter by a microorganism. When released during production, pentane quickly converts into carbon dioxide and water as a result of a photochemical reaction. Unlike chlorofluorocarbons (CFCs) and hydrochlorofluorocarbons (HCFCs), pentane doesn't contain chlorine, so it is not detrimental to the ozone layer.

And although pentane contributes to man-made emissions of volatile organic compounds (VOCs), study shows that these are only found to be at 0 to 0.2% range. Currently, researchers are looking for ways to minimise the use of pentane through the process of recapturing and reusing pentane.
Steam is used as the main energy source during the manufacturing process. Boilers use natural gas as fuels to produce steam. As per Foamex' water consumption, there is relatively low water usage as water is reused several times during production.
The outcome is lightweight polystyrene that provides the following benefits:
- Source reduction and fully recyclable material
- Excellent acoustic and thermal insulation
- Dimensionally stable
- Water, vapour and moisture resistant
- Long-lasting and resilient to premature degradation
- Lightweight material to reduce time and handling costs
With the zero-waste manufacturing policy, Foamex sets a gold standard for expanded polystyrene foam recycling. Polystyrene remnants and cut-offs are collected at the end of every production and reintroduced into the manufacturing process.
Foamex goes to great lengths to ensure that proper manufacturing, delivery, application, maintenance, as well as after-sales service are observed. The team provides all clients with a bag for on-site clean-up where scraps are stored until collected as part of their expanded polystyrene foam recycling program.
With a diligent product research and development team, Foamex works incessantly to improve the processes already in use to further minimise waste and formulate new recycled polystyrene products.
Book an appointment with Foamex and learn more about how they make a difference with their expanded polystyrene foam recycling process. Call 02 9773 1655 or visit www.foamex.com.au.

|